As the demand for advanced batteries continues to grow, the significance of battery slurry in the manufacturing process becomes increasingly apparent. This FAQ article aims to provide a comprehensive understanding of battery slurry, its composition, significance, and manufacturing process.
1. What is Battery Slurry?
Battery slurry, also known as electrode slurry, is a crucial component in the production of batteries. It serves as the primary material used to create electrodes, which are integral to the functionality of various types of batteries, including lithium-ion, lead-acid, and more.
2. What is the Composition of Battery Slurry?
Battery slurry typically consists of several key components:
Active Materials: These are the primary electrochemical components responsible for storing and releasing energy during the battery's operation. Common active materials include lithium cobalt oxide (LiCoO2) for lithium-ion batteries and lead dioxide (PbO2) for lead-acid batteries.
Conductive Additives: Carbon black or graphite are incorporated into the slurry to enhance electrical conductivity within the electrode, facilitating efficient charge and discharge cycles.
Binders: Binders play a crucial role in holding the active materials and conductive additives together, forming a cohesive structure within the electrode. Common binder materials include polyvinylidene fluoride (PVDF) and carboxymethyl cellulose (CMC).
Solvents: Solvents dissolve the binder and create a fluid mixture that can be coated onto electrode substrates. Common solvents include N-methyl-2-pyrrolidone (NMP) and water.
3. Why is Battery Slurry Important?
Battery slurry plays a pivotal role in determining the performance, energy density, and lifespan of batteries. The uniform dispersion of active materials and additives within the slurry directly impacts the electrode's electrochemical properties, influencing factors such as capacity, voltage, and cycle life.
4. How is Battery Slurry Manufactured?
The manufacturing process of battery slurry typically involves several key steps:
Material Preparation: Active materials, conductive additives, and binders are carefully selected and prepared according to specific formulations.
Mixing: The components are mixed together in precise proportions to form a homogeneous slurry. Various mixing techniques, such as high shear mixing or planetary mixing, may be employed to ensure uniform dispersion.
Coating: The slurry is then coated onto electrode substrates, typically made of materials such as aluminum or copper foil, using techniques such as doctor-blade coating or slot-die coating.
Drying and Calendaring: The coated electrodes undergo drying to remove solvent and binder, followed by calendaring to ensure uniform thickness and density.
Assembly: The electrodes, along with separators and electrolytes, are assembled into battery cells, which undergo additional processing before final packaging.
5. What are the Challenges in Battery Slurry Manufacturing?
Manufacturing battery slurry requires careful control of various parameters, including slurry viscosity, particle size distribution, and coating thickness. Achieving uniformity and consistency in slurry composition is essential to ensure the performance and reliability of the resulting batteries. Additionally, environmental considerations, such as solvent choice and waste management, pose challenges in the production process.
6. How to find one-stop solution provider?
Choose ONGOAL TECH as your one-stop solution provider for battery slurry mixing, benefiting from our team's extensive expertise in battery manufacturing technologies, access to cutting-edge innovations tailored to enhance efficiency and quality, customizable solutions to meet your unique requirements, comprehensive support services from installation to maintenance, and a global presence ensuring reliable service worldwide.
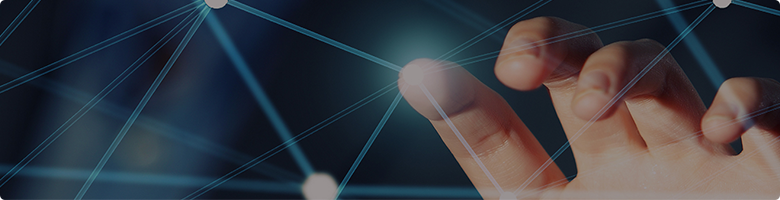
