In the realm of lithium-ion battery manufacturing, the production processes for anode and cathode materials represent distinct yet interconnected facets of battery technology. Anode and cathode materials serve complementary roles in storing and releasing energy within the battery cell, but their production methods and material properties differ significantly. This technical article aims to elucidate the key differences between anode and cathode material production processes, shedding light on the unique challenges and considerations inherent to each.
Anode Material Production:
Anode materials typically consist of carbon-based materials, with graphite being the most commonly used material due to its excellent conductivity and stability. The production process for anode materials begins with the selection of high-purity graphite as the primary raw material. The graphite is then subjected to grinding and purification processes to remove impurities and achieve the desired particle size distribution.
Once purified, the graphite is mixed with binders and conductive additives to form a homogenous slurry. This slurry is then coated onto a substrate, such as copper foil, using techniques such as doctor-blade coating or spray coating. The coated substrate is then dried to remove any solvent and ensure proper adhesion of the active material to the substrate.
After drying, the anode material may undergo further processing steps, such as calendering to improve mechanical strength and conductivity, and sizing to achieve the desired dimensions. The final anode material is then assembled into battery cells, where it serves as the negative electrode in the electrochemical reaction during battery operation.
Cathode Material Production:
In contrast to anode materials, cathode materials are typically composed of metal oxides, such as lithium cobalt oxide (LiCoO2), lithium iron phosphate (LiFePO4), or lithium manganese oxide (LiMn2O4). The production process for cathode materials begins with the selection of the appropriate metal oxide precursor, which is typically synthesized through chemical reactions or solid-state methods.
Once synthesized, the metal oxide precursor undergoes grinding and milling to achieve the desired particle size and morphology. The milled powder is then mixed with conductive additives and binders to form a cathode slurry. This slurry is coated onto a substrate, such as aluminum foil, using similar coating techniques as those employed in anode material production.
After coating, the cathode material is dried to remove solvent and ensure proper adhesion to the substrate. Additional processing steps, such as calendaring and sizing, may be employed to further enhance the mechanical and electrochemical properties of the cathode material. The final cathode material is then assembled into battery cells, where it serves as the positive electrode in the electrochemical reaction during battery operation.
While anode and cathode materials both play crucial roles in lithium-ion battery technology, their production processes and material properties exhibit distinct differences. Anode materials, typically composed of carbon-based materials such as graphite, undergo processes such as grinding, coating, and sizing to achieve the desired properties. In contrast, cathode materials, which are typically metal oxides, undergo synthesis, milling, coating, and drying processes. Understanding these differences is essential for optimizing the performance and efficiency of lithium-ion batteries and advancing the field of energy storage technology.
ONGOAL TECH offers comprehensive solutions for anode and cathode materials, leveraging advanced technologies and expertise to optimize production processes and deliver high-performance materials tailored to diverse applications. With a focus on innovation and quality, ONGOAL TECH streamlines manufacturing, providing clients with end-to-end support from raw material selection to quality control, ensuring seamless integration into battery assembly while empowering clients to drive advancements in energy storage technology.
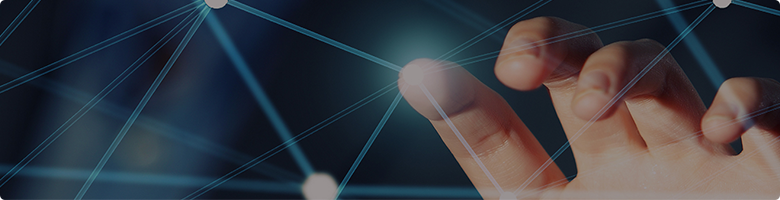
