New High Efficiency Slurry Mixing System
The new high efficiency slurry mixing system adopts the powder and liquid feeding at the same time, and the narrow and long path of the dispersion chamber makes the all slurry pass through the effective dispersion zone.
Solution Features
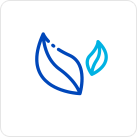
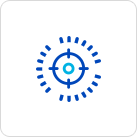
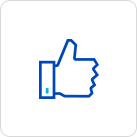
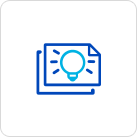
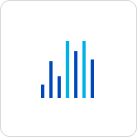
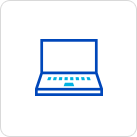
System Display
Models
|
Design Capacity
|
Batch Size
|
Circulating Flow
|
Average Dry
Powder Feed
|
Engine Speed
|
Engine Power
|
YGZJ100
|
100
|
150
|
50
|
10
|
2850
|
37
|
YGZJ300
|
300
|
450
|
200
|
30 | 2000 | 55 |
YGZJ600
|
600
|
900
|
300
|
60 | 2000 | 90 |
YGZJ900
|
900
|
1350
|
450
|
90 | 1500 | 132 |
YGZJ1200
|
1200
|
1800
|
600
|
120 | 1500 | 185 |
YGZJ1500
|
1500
|
2250
|
750
|
150 | 1500 | 200 |
YGZJ2400
|
2100 | 3600 | 1200 | 240 | 1000 | 280 |
Note: The contents in this document are for information purposes only, and the actual product parameters depend on the specific design scheme
Solution Introduction
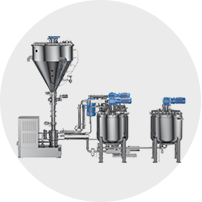
Small size of equipment; integrated binder dissolution function; space narrowing; compatibility and flexibility greatly improved.
01
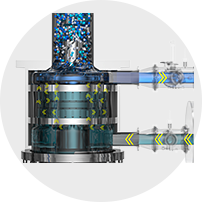
Adopting the bottom-in and top-out structure, the dispersion zone is located below the mixing zone, and under the action of the circulation pump, the slurry is kept 100% filled in the dispersion zone, which greatly reduces the risk of foaming.
02
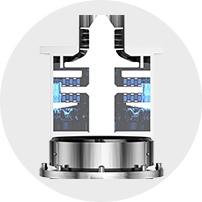
The cooling area of the dispersing cavity is more than 300% larger than that of
the peer. Impeller diameter is small, with the same pulping efficiency, the temperature rise rate drops dramatically.
03
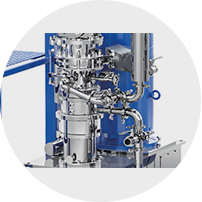
Due to the large impeller structure in the traditional design, process magnifies the
risk and the cost is high. The decentralized module of this product is multi-layer
stacking design, which capacity can achieve from 100L to 3000L or even larger,
so as to solve the bottleneck of production capacity.
04
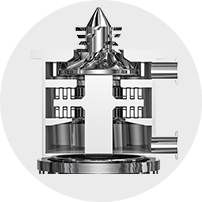
The system adopts separate channel design for mixing and dispersing functions,
and material wets and thins before mixing and discharging, which can solve the problems such as fast discharging, easy back flow and overload caused by the traditional stack structure design of discharging and dispersing devices.
05
Customer Stories

