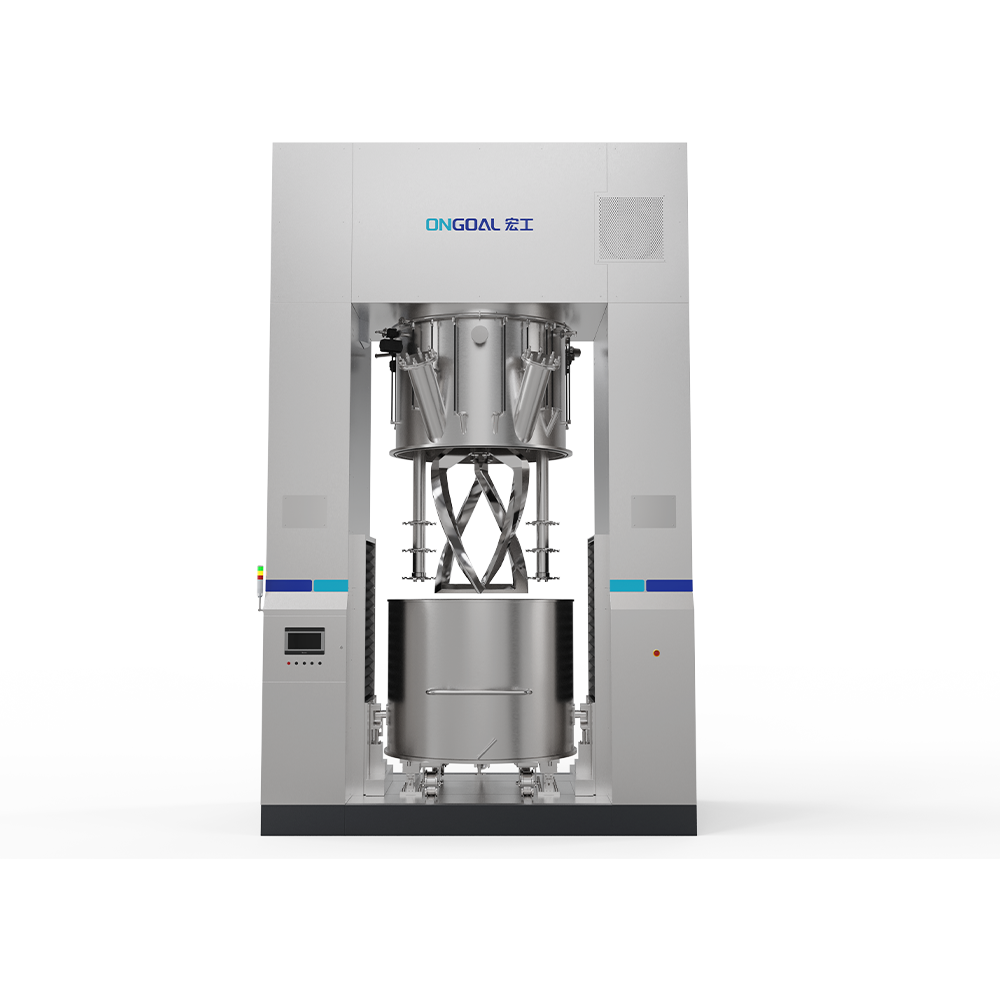
Dual Planetary Mixer
Used for mixing, homogenization and dispersing of powder and liquid materials. The dispersing disc and stirring paddle realize revolution and rotation simultaneosly. The speed can be adjusted by the frequency converter. The special mixing method makes the materials strongly dispersed and pressed to ensure materials fully dispersed and mixed.
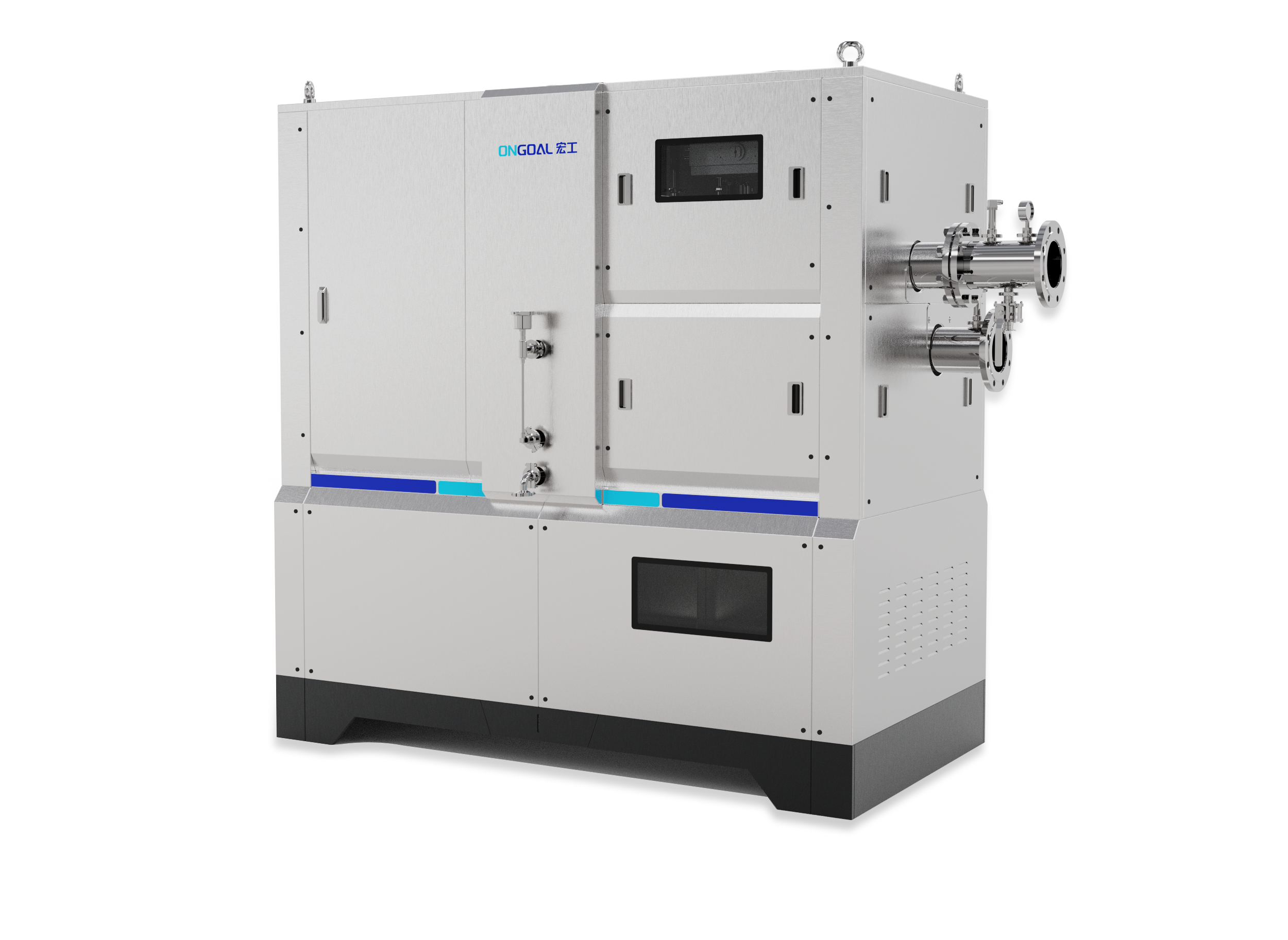
High Efficiency Slurry Mixing System
The new high efficiency slurry mixing system adopts the powder and liquid feeding at the same time, and the narrow and long path of the dispersion chamber makes all slurry pass through the effective dispersion zone.
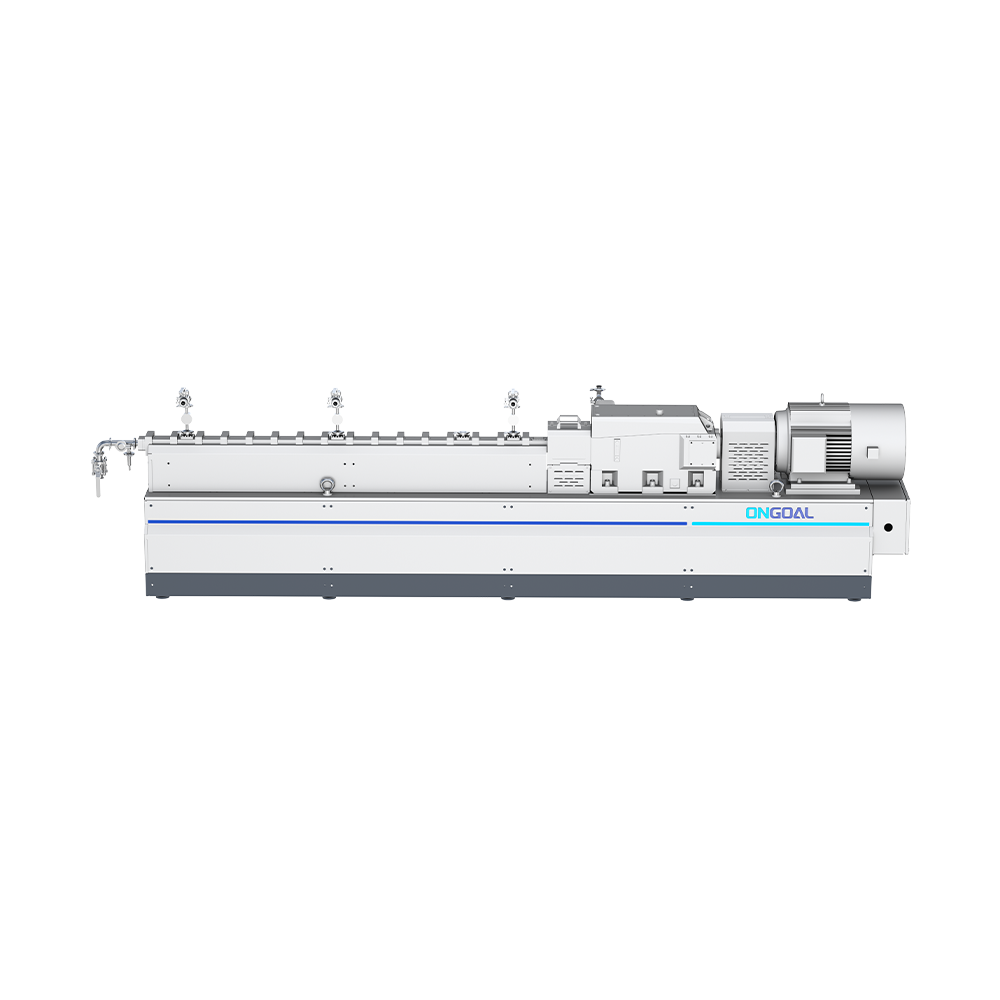
Twin-screw Continuous Slurry Mixer
As the core of the twin-screw slurry mixing system, it adopts a continuous slurry mixing process to help improve the consistency and stability of lithium batteries. The equipment adopts modular twin-screw structure, integrating conveying, mixing, dispersing and exhausting in one, which can realize free collocation of functions and satisfies the demand of different working conditions to solve the problem of cost and energy loss caused by a single limited function.
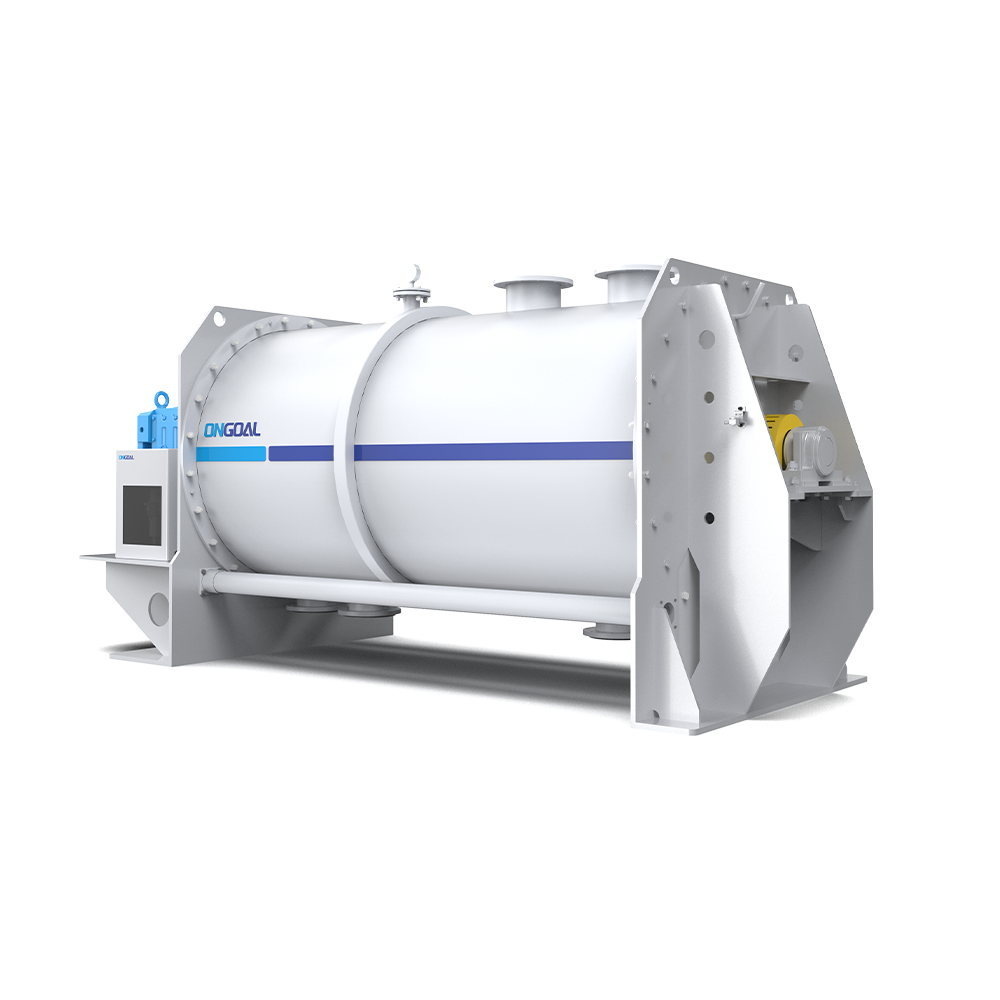
Ribbon Mixer
Ribbon mixer is used for mixing powders, powder & liquid, especially for the viscous paste materials or high gravity material. Because of the difficulty of cleaning viscous materials, it is more suitable for the occasion of large output and infrequent change of varieties.
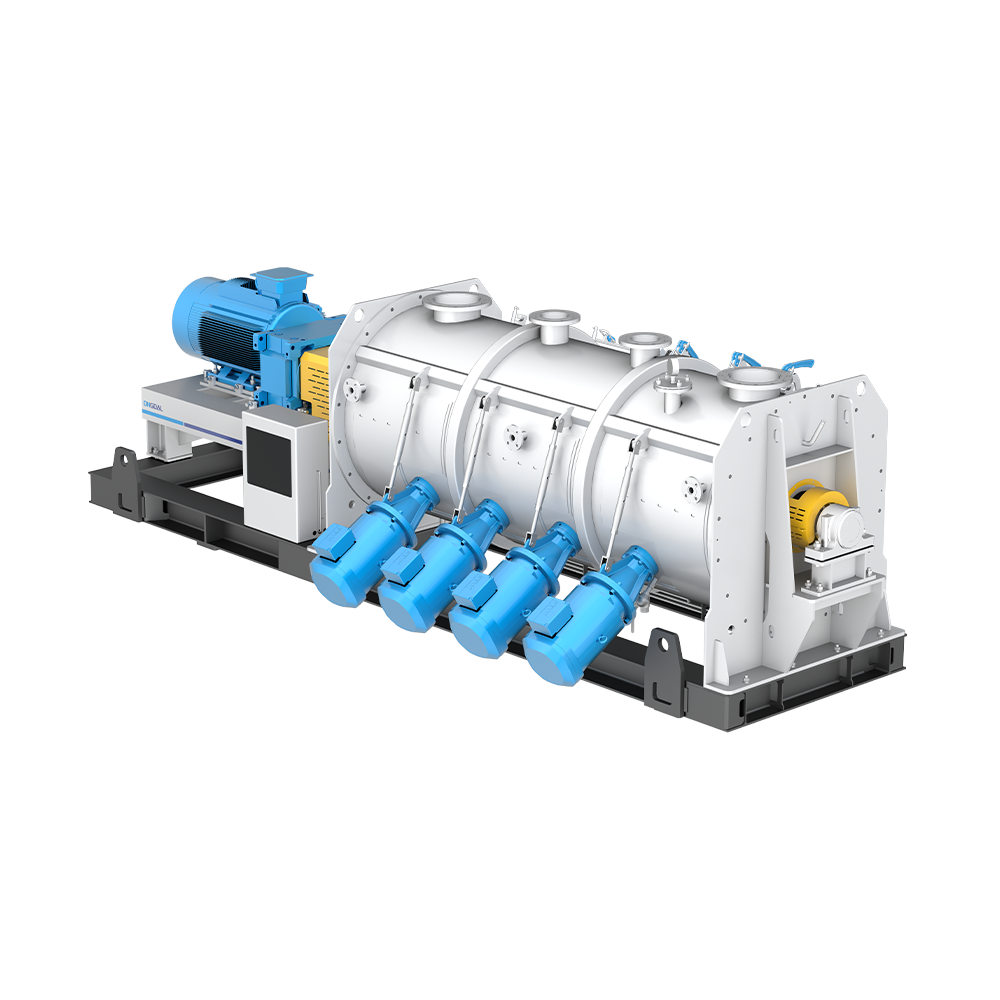
Ploughshare Mixer
Ploughshare mixer is mainly used for high-efficiency mixing of powder. The stirring shaft is fixed on the horizontal drive shaft by a bracket and rotates along the wall to make the materials diffuse and shear with each other and achieve better mixing efficiency.
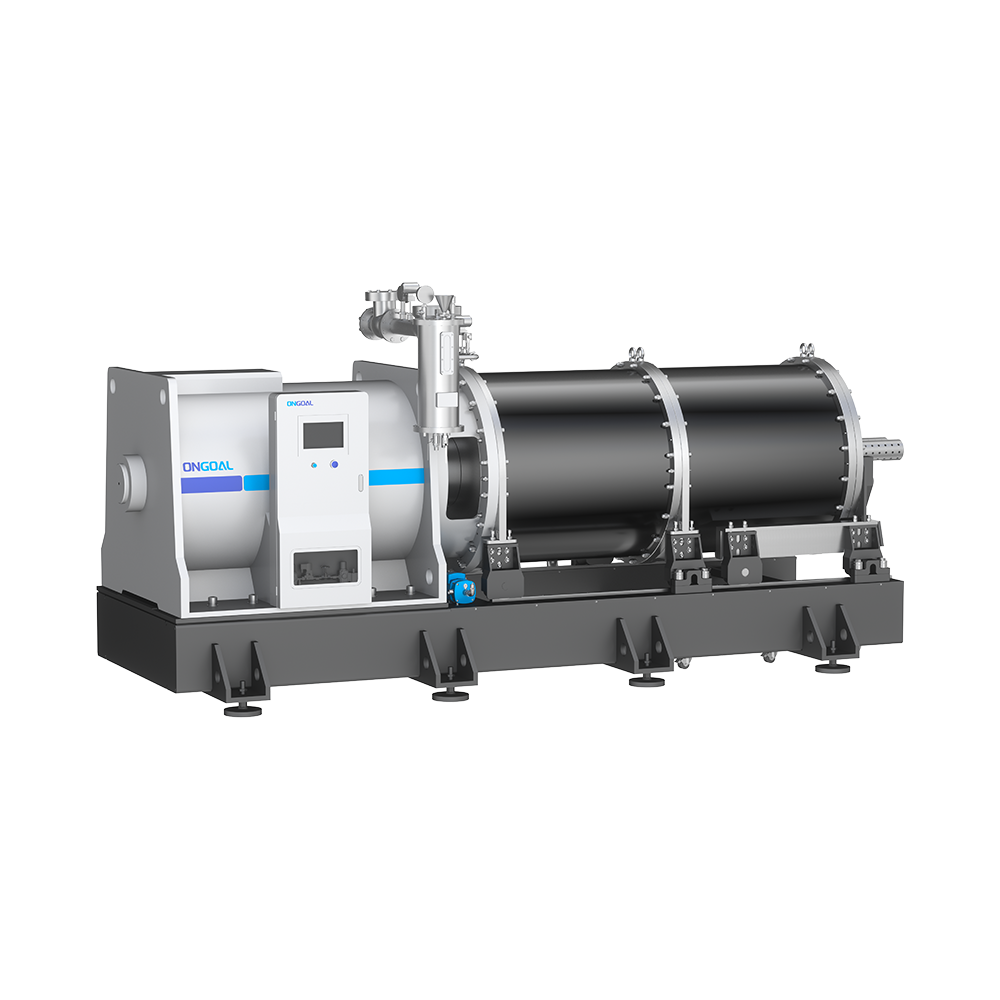
Rod-pin Bead Mill
SDBP series permanent magnet direct drive rod-pin bead mill is a professional grinding equipment developed by ONGOAL for battery materials. It adopts rod-pin structure with high energy density, fully automatic dosing system to ensure continuous production of grinding, providing continuously high efficiency nano grinding
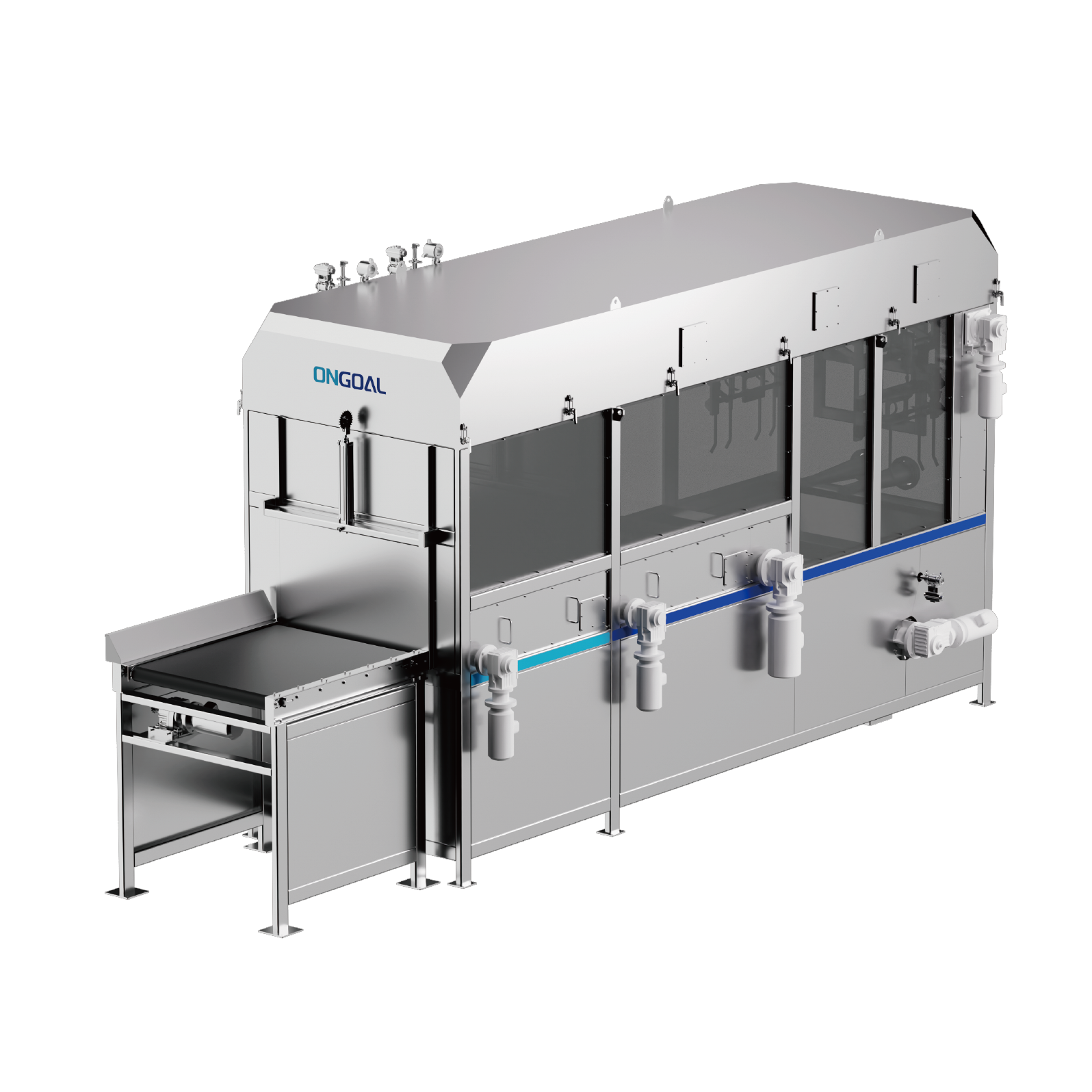
HQDC Fully Automatic Big Bag Unloading Machine
The fully automatic big bag unloading machine is suitable for unloading powder and granular materials in various types of big bags. its fully enclosed working environment ensures a clean and efficient production process. Equipped with an intelligent control system featuring visual operation, the machine can automatically unload and discharge materials in bulk.
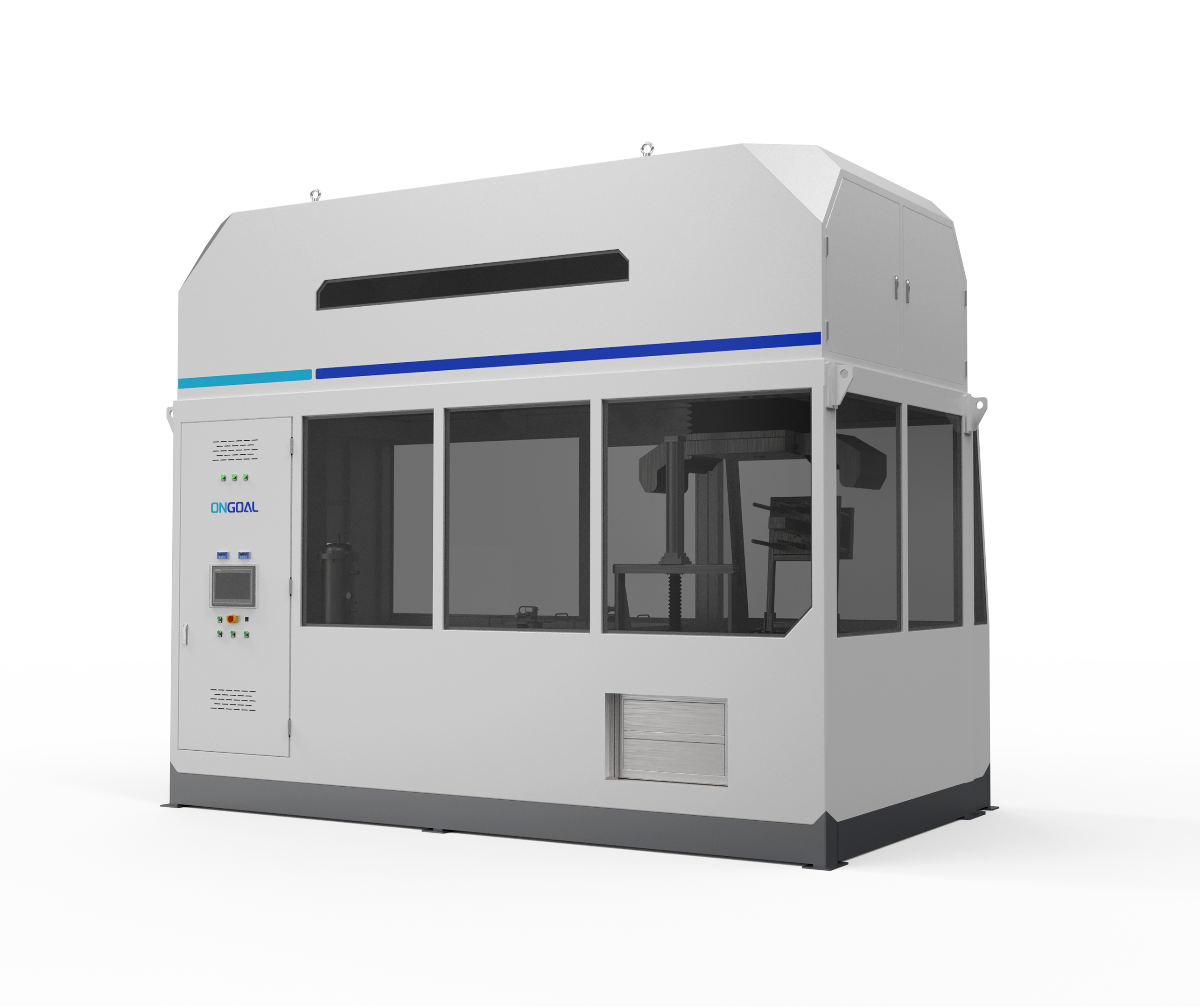
Fully Automatic Big Bag Unpacking Machine
It is primarily used in fully automatic continuous unpacking of 300-1000kg bagged materials. It accomplishes automatic feeding, clamping, workstation circulation, pallet retrieval, bag gripping, bag breaking, bag shaking for material discharge, and waste bag recovery.
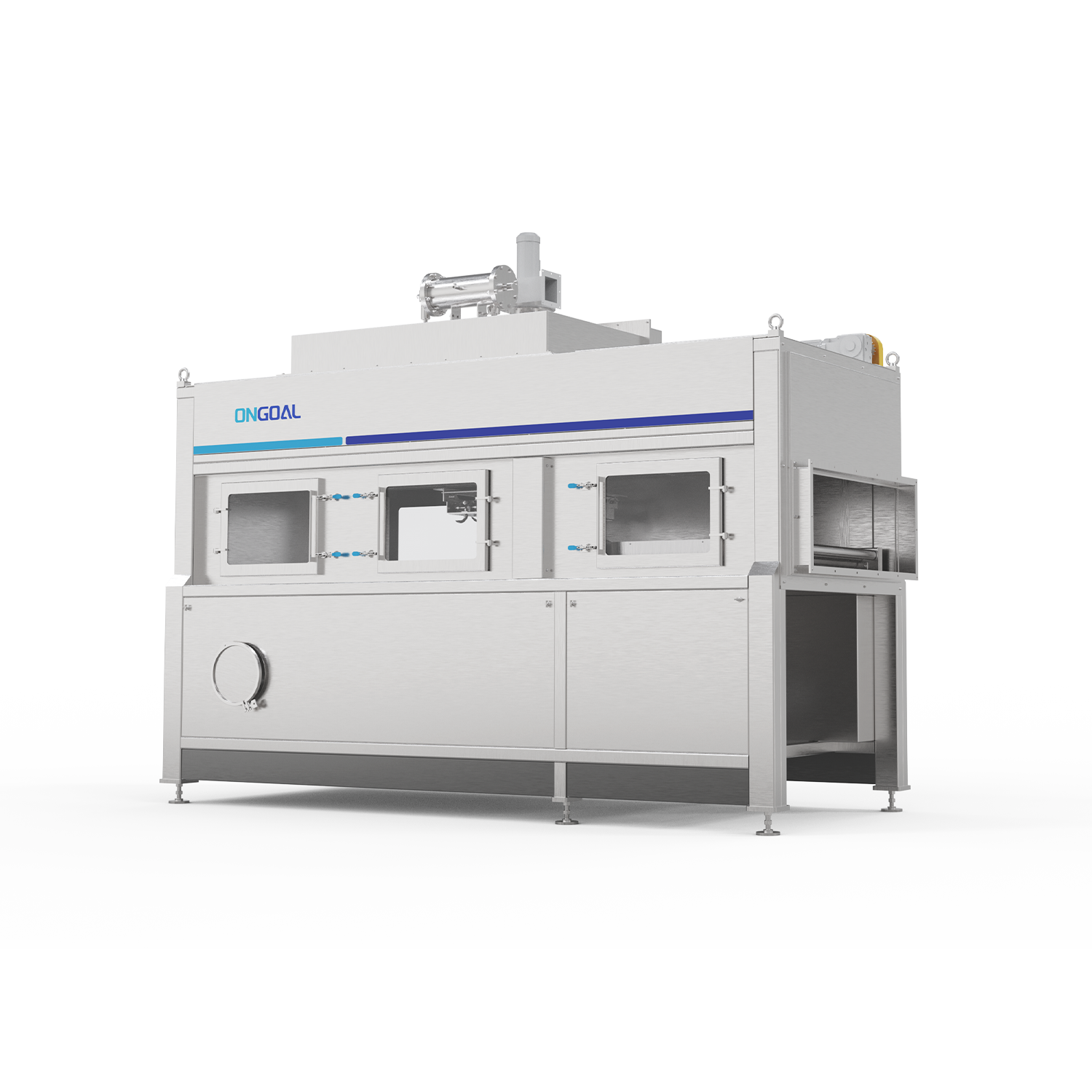
Automatic Small Bag Unloading Machine
The small bag unloading machine is mainly used for the automatic unpacking of small bags of materials weighing around 25kg, enabling automatic and continuous production. It boasts advantages such as low residue rate, no dust overflow, and efficient operation, making it suitable for batch automatic unpacking and unloading requirements in various industries.
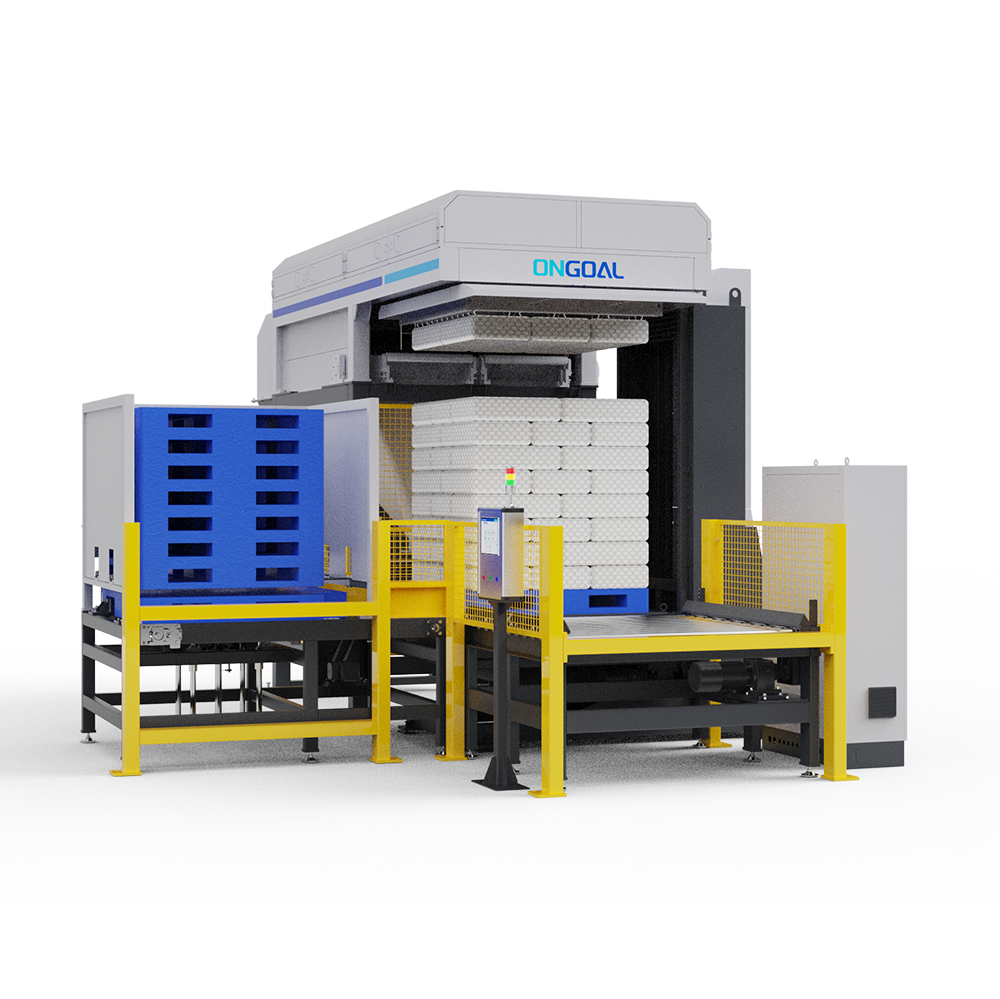
Layer By Layer Debagging Machine
The small bag unloading machine (layer by layer) is suitable for batch unpacking of 25kg bagged powder and granular materials. It greatly improves productivity, reduces labor intensity, and achieves large-scale, high-efficiency automated production by unpacking the stacked small bags layer by layer.
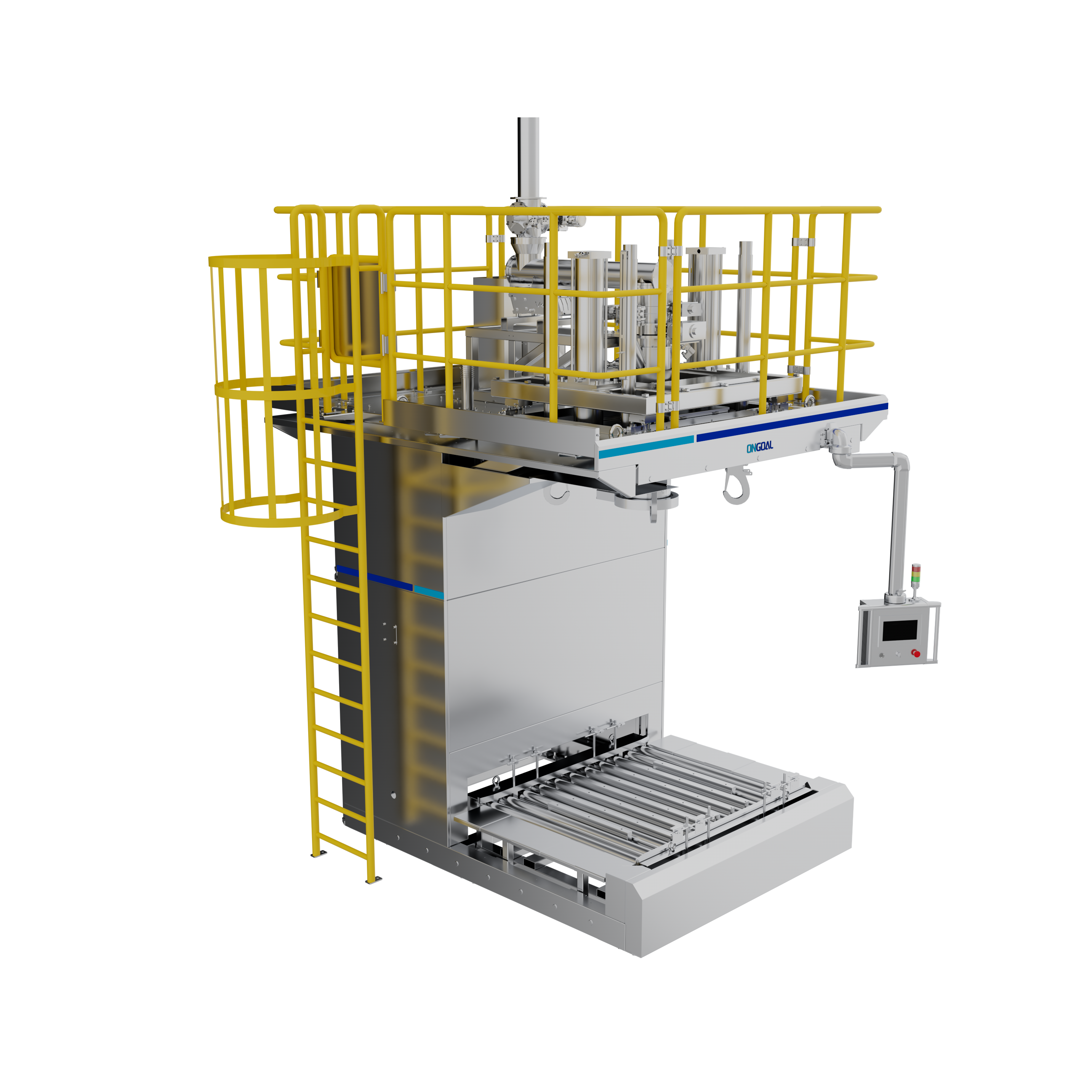
Big Bag Packing Machine
Integrated Big Bag Packing Machine is used for packaging big materials with large capacity. It adopts vertical cantilever integrated design and integrates functions of automatic peeling, bag inflating, spiral feeding, sampling, metering, double-check,vibration, heat sealing, automatic conveying, etc.
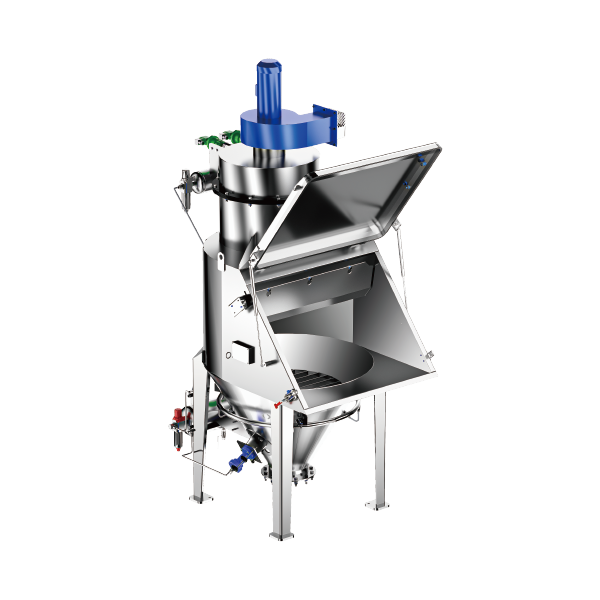
Small Bag Unloading Station
It is mainly applied in small bag unloading and material feeding. Different models are available to suit on-site environment, plant layout, process and material characteristics.