What is Jet Mill?
Jet mills are instrumental in the production of battery materials by employing a high-speed stream of compressed air or inert gas to refine particles through impact. These mills are designed to generate particles that meet specific size criteria, with larger particles being further milled until they achieve the desired size, resulting in a precise and uniform particle size distribution in the final product.
What is the process?
Within the mill, particles are drawn towards the periphery based on the square of their radius or diameter. Larger particles continue to be milled until they are small enough to remain in the mill's central zone, which is where the discharge port is located.
After the milling process, particles are separated from the gas stream efficiently through cyclonic separation. The jet mill's design consists of a short and wide cylindrical structure, with the cylinder's height being less than its diameter. Compressed gas is injected through nozzles positioned tangentially to the cylinder wall, creating a vortex that facilitates the milling process. The gas is then discharged through a central tube aligned with the cylinder's axis.
What contributes to battery material efficient grinding?
l Energy Efficiency
Jet mills are known for their low energy consumption due to an optimized nozzle design that reduces air consumption and energy usage. The three-nozzle arrangement minimizes energy loss from air flow collisions, potentially saving up to 50% of the air consumption compared to other models, thereby reducing energy costs.
l Particle Size Distribution
The grading wheel's structure and positioning are fine-tuned to improve the quality and efficiency of the final particle size distribution. The vertical orientation of the grading wheel leads to a more focused particle size distribution and allows for more accurate control.
l Clean Operation
The equipment is designed to operate without contact with magnetic foreign materials, keeping the increase of foreign matter during the grinding process to ≤ 10ppb. The use of a full ceramic structure in the grading wheel and nozzles minimizes the introduction of metal contaminants, preserving the material purity needed for battery applications.
l Advanced Control Systems
The mill features fully automatic control with an intuitive user interface, enabling one-touch start-stop operations and real-time central monitoring, which enhances control and efficiency over the production process.
l High Product Qualification Rate
The implementation of labyrinth and gas sealing technologies effectively prevents the escape of oversized particles, leading to a high qualification rate of finished products.
l Equipment Design Optimization
Extensive simulation experiments have led to the optimal selection of nozzles, grading wheels, chamber structures, and matching sizes and parameters. These optimizations have significantly reduced both energy consumption and the crushing rate, leading to more efficient milling operations.
Introducing ONGOAL TECH Jet Mill:
At ONGOAL TECH, based on head client practices, our LQM series Jet Mill is engineered to meet the exacting standards of the battery material production industry. Our innovative design and advanced technologies not only ensure an efficient and clean grinding process but also contribute to the production of high-quality materials that are essential for the next generation of battery technology. With a focus on sustainability and performance, ONGOAL TECH Jet Mill is the choice of forward-thinking manufacturers seeking to push the boundaries of battery material innovation.
Find LMQ Jet Mill here
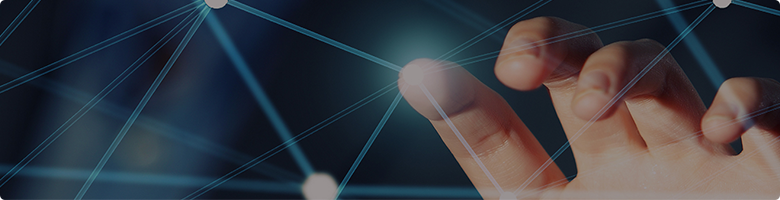
