When it comes to selecting an industrial mixer, making the right choice is paramount for optimizing your operations. Here's a rundown of crucial considerations to ensure you're getting the perfect fit:
Operating Environment: Dive deep into the operational data, including material characteristics (dry, wet, paste, mastic compound), capacity needs (volume or weight), component properties, and other attributes like density, viscosity, and granule size.
Temperature Management: Stay ahead of the game by factoring in temperatures during the mixing process to guarantee smooth operation and product integrity.
Mixing Intensity: Tailor the mixing intensity to match your material requirements, whether you need a gentle blend or a vigorous mix for optimal results.
Operating Mode: Decide between batch or continuous production based on your workflow, ensuring seamless integration with your existing processes.
Drive and Power Supply: Choose the right drive type (pneumatic, hydraulic, or electric) and specify power supply requirements for a seamless fit into your facility.
Enclosure and Jacketing: Ensure your mixer is housed in the appropriate enclosure (standard or explosion-proof) and consider additional heating or cooling features to maintain optimal conditions.
Discharge Options: Specify how you want your final product to be discharged—whether it's free-flowing powder or liquid, or if it requires special handling.
Material Contact and Surface Finish: Pay attention to material contact parts and surface finishes to meet hygiene or industrial-grade standards, ensuring product safety and longevity.
By carefully evaluating these factors, you'll not only find the ideal mixer for your needs but also streamline your production process. And with ONGOAL TECH's customized solutions, your journey to optimized production is made even smoother.
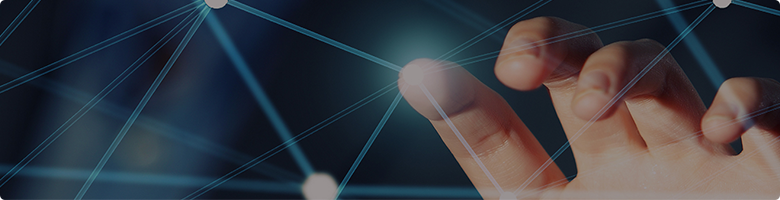
