The feeding and packing processes have always been major challenges in achieving fully automated production lines for battery materials. ONGOAL TECH has recently introduced the fully automatic big bag unpacking machine and the fully automatic big bag packing machine, empowering the front and back ends of material production lines with automation intelligence to assist in realizing "unmanned factories."
On the afternoon of April 11th, at the 2024 China Qingdao Lithium Battery Anode Material Technology Conference, Will Jiang, the Design Director of the Battery Materials BU at ONGOAL TECH, delivered a speech entitled "Upgrade of Material Production Line Automation Intelligence."
He mentioned that with the rapid development of battery manufacturing, dust and pollution during the production process have become pain points in the industry. Especially in the feeding and packing processes, traditional manual intervention has led to low production efficiency and serious environmental pollution, making it a challenge for fully automating battery material production lines. ONGOAL TECH, driven by technological innovation, has brought about a new upgrade to the automation intelligence of battery material production lines.
Fully Automatic Big Bag Unpacking Machine
1. High costs of manual intervention? -Achieving fully automated unpacking processes
Traditional big bag unpacking processes require significant manual intervention, resulting in high production costs, while the negative impacts of the working environment and labor intensity on personnel cannot be ignored. ONGOAL TECH has designed a series of fully automated processes, including scanning code input, automatic bag grasping, bag transfer and breaking, bag shaking, and bag recovery, greatly reducing the pain points and uncertainties caused by previous manual interventions.
For example, in the automated non-destructive bag grasping process, it can fully adapt to various materials such as conventional, semi-packed, stacked, gas-expanded, and gas-reduced materials, ensuring that the big bags remain intact and have good material adaptability. Moreover, after 3568 cycles of lifting and grabbing tests, the success rate of lifting and grabbing is 100% even when the big bag and pallet are randomly positioned and rotated.
2. Is pollution inevitable in the production line? -Dust-proof, spill-proof, and foreign-object-proof measures
Dust pollution and foreign object control have always been challenges in the unpacking process. ONGOAL TECH has implemented efficient dust control through methods such as fully enclosed micro-negative pressure design, independent dust removal at each workstation, and variable-frequency and time-sharing control of air volume, ensuring a clean production environment and the health and safety of employees.
Additionally, the setting of external bag cleaning equipment strictly controls magnetic and non-metallic foreign objects. The bag-breaking method uses a C-shaped knife, which produces no visible debris compared to the methods using cross knives or rotating disc knives. After bag recovery, the residual process is strictly controlled, with a residual material ratio of about 0.02%.
Fully Automatic Big Bag Packing Machine
1. Is manual involvement unavoidable in the process? -Achieving fully automated packing processes
ONGOAL TECH's fully automatic big bag packing machine integrates functions such as automatic pallet and big bag placement and replenishment, automatic bag opening and bagging, automatic material sampling, automatic re-inspection, automatic vacuuming and heat sealing of big bags, automatic labeling, and storage.
For example, the automatic bag supply system for packing bags can handle various big bag styles while reducing the space occupied by big bag storage, making it easier to integrate with AGVs and completely replacing manual tasks such as picking up big bags, bagging, and sealing bag mouths.
Based on a calculation of personnel configuration for a 10WT/year artificial graphite production line with 10 packing machines and three shifts, ONGOAL TECH's fully automatic big bag packing machine solution can save approximately 54 personnel.
2. Poor packing consistency? -High consistency of the final product
Another technical challenge in the packing process is the poor consistency of packing product quality. During the packing process, we achieve non-destructive bag opening and bagging, ensuring consistency and quality stability of samples through automatic sampling, packing, and sample point-to-point delivery.
By using negative pressure conveying technology, samples are accurately transported to the testing room, avoiding manual operation, and improving production efficiency and the controllability of sample quality.
ONGOAL has successfully solved the "last mile" problem of automation intelligence in production lines, not only optimizing the production process but also deepening our understanding and application of production processes. In the future, we will better meet industry customers' environmental requirements and stringent product quality standards, and address industry challenges with better services and innovative solutions.
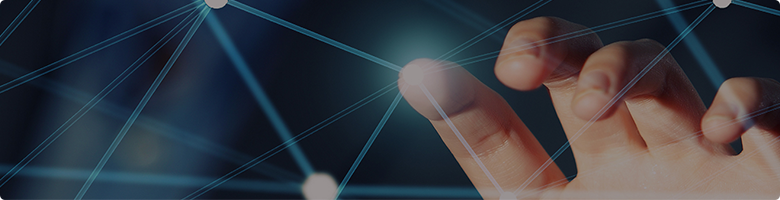
