In the realm of battery production, meeting industry requirements for metal-free is paramount. ONGOAL presents a comprehensive solution that addresses these demands while incorporating cutting-edge technologies to enhance efficiency, precision, and quality. From ensuring ceramicization and minimizing magnetic material intake to implementing closed-loop systems and large-scale production capabilities, ONGOAL is reshaping the landscape of battery material production. Let's delve into the features and advantages of ONGOAL's solution, along with an overview of advanced coating technologies that further optimize the production process.
Meeting Industry Requirements
Battery material production demands adherence to strict industry requirements, focusing on metal-free. ONGOAL's solution encompasses these aspects by ensuring complete ceramicization, minimizing magnetic material intake to less than 30PPB, and implementing closed-loop systems to maximize resource efficiency. Additionally, the system boasts large-scale production capabilities, enabling high hourly capacities for various materials such as ternary materials, lithium cobaltate, and lithium manganese oxide, among others.
Enhanced Efficiency and Precision
The transition from traditional vertical cone mixing equipment to horizontal mixers represents a significant leap in efficiency and precision for ceramic battery production. ONGOAL horizontal ploughshare mixers offer superior mixing efficiency, higher quality output, shorter unloading times, and reduced residue, thereby streamlining the production process and enhancing environmental sustainability. Moreover, these mixers facilitate closed, sealed processing, minimizing external environmental impacts and ensuring optimal material handling.
(Production line for NCM)
Advanced Coating Technologies
In addition to process optimization, the utilization of advanced coating technologies further enhances the performance and longevity of ceramic battery components. Tungsten carbide coating, renowned for its high hardness, wear resistance, and corrosion resistance, significantly improves component durability and lifespan. The key performance indicators for tungsten carbide coatings include high hardness (HV1150+), strong bonding strength (68MPa+), low porosity (less than 1%), and minimal oxide content (less than 3%), ensuring reliable performance in harsh operating environments.
Nano-ceramic coating technology, incorporating active metal micro-powders, nano-ceramic powders, and rare earth powders, offers superior temperature resistance, durability, and corrosion resistance. These coatings exhibit high thermal stability, exceptional hardness, and resistance to thermal shock, making them ideal for ceramic battery applications. Additionally, their corrosion resistance properties make them suitable for a wide range of chemical environments, ensuring long-term reliability and performance.
Conclusion
ONGOAL's comprehensive solution for battery production combines advanced technologies with industry-leading expertise to deliver unparalleled efficiency, precision, and quality. By meeting stringent industry requirements, optimizing production processes, and incorporating advanced coating technologies, ONGOAL empowers manufacturers to achieve new heights in battery material production. With a focus on safety, sustainability, and performance, ONGOAL is shaping the future of battery technology, driving innovation, and excellence in the industry.
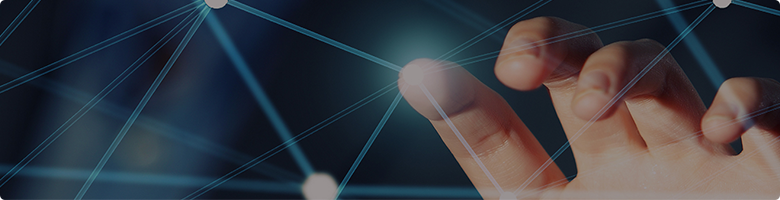
