Different powders and granules are used in the production process of paint. Limited by the characteristics of the materials, the problems of dust and pollution are accumulating. The paint powder automatic conveying and dosing system provided by ONGOAL Tech for paint production is targeted to solve the problems of paint production and help customers realize manufacturing upgrade.
Industry pain points:
- Low capacity and high fluctuation of traditional process
- Prominent problems of pipe clogging and powder leakage
- Serious problems of dust and pollution in the production process
- High labor intensity and more manual intervention
System advantages:
- Energy saving and environmental protection, high production efficiency
- Sealed production, no dust
- Automated production to reduce labor intensity
- Stable product quality to reduce the influence of human factors
Paint production requires a large number of powder and granular materials, with a wide variety of materials and complex characteristics. The automatic material conveying and batching system designed by ONGOAL Tech for the paint industry is generally composed of several sections such as feeding, storage, conveying, metering and dust removal.
Dust-free feeding and centralized storage management
The powder and granular materials used in the paint industry mainly include pigments and fillers, mostly in the pack of tons or small packages, and some large quantities of raw materials are transported by tanker truck. Traditional production process mostly adopts manual unpacking directly into the mixing kettle, with high labor intensity and serious environmental pollution.
ONGOAL provides ton bag unpacking station and small bag unpacking station, equipped with single point dust removal device or central dust removal system, no dust is raised for feeding.
The tanker truck unloading and system are connected by fully enclosed connection to avoid dust spreading to the workshop.
After the feeding is completed, the raw material storage is managed centrally, and according to the material characteristics, centrifugal silo and activation hopper are selected to ensure the smooth material discharging.
Clogging-proof pipe for large volume conveying
According to the characteristics of different materials, ONGOAL provides precise conveying optimization design for paint production.
Take quartz and colored sand raw materials required for the production of lacquer and colorful paint as an example, because of the hardness and abrasiveness of the materials, the design adopts the positive pressure dense phase pneumatic conveying to send the materials to the back section of the equipment.
ONGOAL original low-speed dense-phase positive pressure conveying system has the reliability of long-distance conveying and large conveying capacity, and can minimize the influence of materials on the pipeline during conveying.
Variable frequency speed control clogging-proof design: the conveying process real-time monitoring of the pressure changes in the conveying pipeline, when an abnormal increase in pressure in the pipeline is detected, the control system dynamically adjusts the front-end feeding device frequency control speed until the pressure value of the pipeline unclogging returns to normal level to avoid clogging of the pipeline.
Precise metering to meet the production needs
With rich experience in system integration, ONGOAL adopts weight gain dosage, weight loss dosage, dynamic multi-component dosage and loss-in-weight dosage according to different working conditions, with precise metering and stable efficiency.
For small batch, multi-variety, and personalized production requirements, we can provide small material dosage system combined with pneumatic conveying method, which can improve the flexibility of process adjustment and avoid the influence of human factors on product quality.
Automated Process Management
The system is equipped with a production management system, which can start production with one key according to the recipe, or be independently controlled by a separate module system, and each part can be independently selected for automatic control or manually triggered operation to meet the actual production needs.
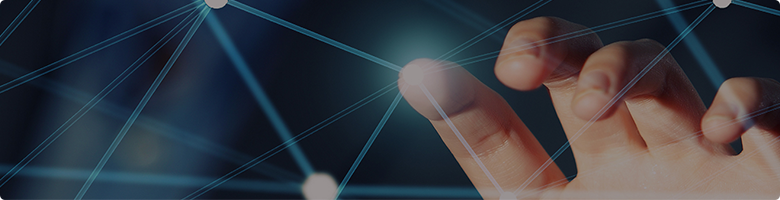
