Despite being in use for less than three months, frequent issues with ploughshare mixers have led to production line shutdowns.
What overlooked details have caused such significant problems?
1. Ceramic Liner Detachment
Issue Description:
Ceramic liners glued to the interior have gaps and tend to fall off easily. During operation, many ceramic pieces detached, causing metal exposure and contamination of production materials, leading to production line shutdowns.
Solution:
ONGOAL TECH's ploughshare mixer features an industry-first interlocking ceramic liner design. The liners are tightly locked with no gaps, ensuring they do not fall off and have a long service life.
2. Frequent Wear and Replacement of Parts
Issue Description:
Ploughshare heads' coatings flake off within three months of use. After repair, the coating quality is poor, leading to large-scale detachment. High-speed components like fly knives, using metal plus tungsten carbide coating, wear out quickly, increasing magnetic contaminants. Pure tungsten carbide components have poor toughness, resulting in frequent quality issues and low lifespan.
Left: Flying Knife Wear Details / Right: ONGOAL Pure Zirconia Flying Knife
Solution:
ONGOAL TECH's ploughshare mixer uses industry-first pure zirconia material for fly knives (shown in the material display, also featuring titanium alloy cap nuts), offering high toughness and wear resistance, reducing maintenance and replacement frequency, and enhancing overall durability.
3. Short Seal Lifespan and Monitoring Challenges
Issue Description:
Mechanical seal failure results in powder leakage from the shaft end, with repairs not effectively resolving the issue. Multiple customer feedbacks indicate high leakage risk due to poor main shaft sealing.
Solution:
ONGOAL TECH's ploughshare mixer features three patented seals for the main shaft, fly knife, and discharge port. These patented seal structures provide stable and long-lasting effects, ensuring no material leakage during operation. The equipment also includes a visual design with 10 sensors for real-time monitoring of equipment and seal status.
Application Cases
Model: 3000L
- Material Type: Ternary Cathode
- Application Process: Pre-sintering Mix 1
- Mixing Time: 1500s (25 minutes)
Model: 2000L
- Material Type: Ternary Cathode
- Application Process: Pre-sintering Mix 2
- Mixing Time: 1800s (30 minutes)
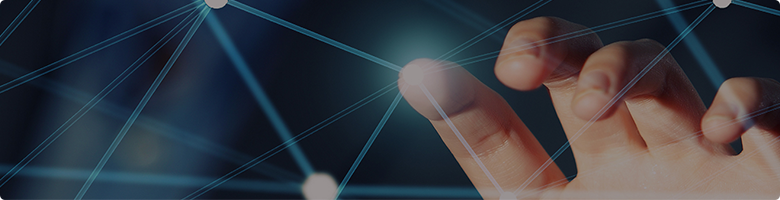
