Mixing the right lithium battery slurry is a real challenge! Every lithium-ion battery production and manufacturing process begins with the preparation of the suspension that becomes the so-called electrode slurry.
This slurry is a mixture of active material, conductive additives, a solvent, and a polymer binder. These materials must all be mixed in a mixer. To explain the urgency of selecting an appropriate mixer, we must first explain the meaning of electrode slurry itself.
What is electrode slurry? It is essentially electrode material dispersed in an organic solvent. The electrode slurry prepared for the following step is applied to copper and aluminum foil, dried, and calendered. This foil, together with the applied slurry, serves as the cathode and anode.
As the slurry system (oil-based, water-based) is different, its properties must be very different. However, it is judged mainly by 3 key factors.
1. Viscosity of the slurry
Viscosity is a fluid flow force on the internal friction phenomenon of a representation. which is used to characterize the nature of the liquid-related resistance factor. Viscosity is also divided into dynamic viscosity and conditional viscosity.
2. Slurry properties
Slurry is is a solid-liquid mixed fluid, in order to meet the requirements of the following coating process, the slurry needs to have the following three characteristics.
① Good fluidity. Flowability can be observed by stirring the slurry and letting it flow down naturally to observe its continuity. The fluidity is related to the solid content and viscosity of the slurry.
②leveling. The leveling of the slurry affects the flatness and uniformity of the coating.
③Rheology. The rheology refers to the deformation characteristics of the slurry in the flow, and it affects the quality of the pole piece.
3. Slurry dispersion basis
The preparation of slurry will generally go through the following stages.
① Dry powder mixing. Feed the raw materials and mix it.
② Slurry kneading stage. At this stage, after the dry powder is mixed evenly, binder liquid or solvent is added and the raw material is wetted and mud-like. After the strong mixing of the mixer, the material is subject to mechanical force shear and friction, while there will also be internal friction between the particles, in each force, the raw material particles tend to be highly dispersed. This stage has a crucial impact on the particle size and viscosity of the finished slurry.
③Dilution and dispersion stage. After the kneading is completed, the solvent is slowly added to adjust the viscosity and solid content of the slurry. At this stage, dispersion and agglomeration coexist and finally reach stability. At this stage, the dispersion of the material is mainly affected by mechanical force, the frictional resistance between powder and liquid, high-speed dispersion shear force, and the interaction force between the slurry and the container wall impact.
For the battery industry, the intelligent homogenization production system specifically designed by ONGOAL is composed of a raw material dosing system, a slurry mixing system and a dispersion and transfer system, including the storage, metering, conveying, stirring, and dispersion of raw materials (powder, slurry, and solvent) and slurry conveying. Among them, the slurry mixing system can provide three kinds of different pulping process equipment, including dual planetary slurry mixer, high efficiency slurry mixing system, and twin-screw slurry system, to meet the production needs of different processes.
Used for mixing, homogenization and dispersing of powder and liquid materials. The dispersing disc and stirring paddles realize revolution and rotation simultaneously. The speed can be adjusted by the frequency converter. The special mixing method makes the materials strongly dispersed and pressed to ensure materials are fully dispersed and mixed.
NEW HIGH EFFICIENCY SLURRY MIXING SYSTEM
The new high efficiency slurry mixing system adopts the powder and liquid feeding at the same time, and the narrow and long path of the dispersion chamber makes sure all slurries pass through the effective dispersion zone.
The equipment adopts a modular twin-screw structure, integrating conveying, mixing, dispersing, and exhausting in one, which can realize continuous material processing and continuous discharging, and realize free collocation to meet the demand of different working conditions and lower cost and energy loss caused by a single function.
Upgrading from PD mixer, ONGOAL become one of the few corps in the industry mastering three kinds of slurry mixing process equipment at the same time. What’s more, it is a huge breakthrough in the industry that the slurry mixing system completes the entire batch mixing in just 1.5 hours with powder feeding, liquid feeding and high efficiency slurry mixing. In the future, ONGOAL will continue to upgrade its technology to provide more advanced solutions for the battery industry.
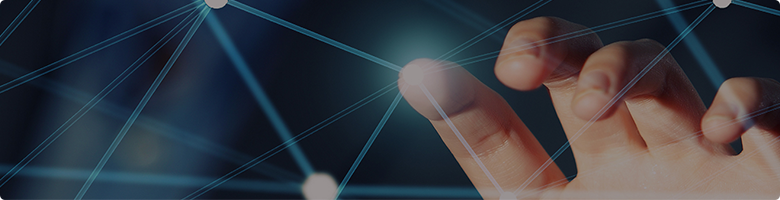
