As one of the effective solutions for white pollution, biodegradable products are gradually walking into our life. In the context of the dual trend of Carbon Neutrality and Restricting Plastic Order, how to put the mastered biotechnology into mass production has become an urgent issue.
Recently, a biodegradable resin project with a total of 16 production lines came into operation, for which ONGOAL TECH provided a one-stop solution including software and hardware equipment, helping the production of degradable plastics to move towards automation, intelligence and scale up.
System benefits
- Enhanced digital management of the workshop
- Smooth and stable operation and high capacity
- More economical and efficient operation
- Scalable and expandable production management system
- Minimal human error
High-volume, automated factory
The project is divided into 8 main areas: Material Feeding Area, Dehumidification & Drying Area, Metering Area, Super Mixing Area, Extrusion Area, Product Crystallization Area, Automatic Packing Area, and Automatic Packing Area.
The areas are well laid out and run smoothly and steadily. ONGOAL system connects the upstream and downstream process sections, collects real-time data and the status of equipment throughout the production line, and dynamically manages the entire production process.
Project site operating touchscreen
A total of 16 production lines are in operation and only about 8 operators are required. The operators only need to confirm the production task list via the touch screen on-site to operate the lines. The workshop runs orderly and avoids the difficulties of managing complex processes.
Digital management with full process traceability
The central control room of the project is like the "brain" of the whole system and is the center of integrated management. With the help of the ONGOAL system, all equipment and processes are centrally controlled through the central control system, and the equipment operates on its own after being programmed.
Central control room
The strict control of raw material quality is essential for high-quality products. The system minimizes human error and enables the collection and traceability of data parameters during the production process, whether it is the main material, the auxiliary material or the liquid material.
For example, the accuracy of the raw materials is confirmed by the scanning gun when feeding, and the storage of each raw material in the tank is completed, providing the primary guarantee for subsequent production.
Bulk bag feeding area
At the same time, production control instructions are given and parameters are modified with the corresponding operating rights. Different rights for operators, engineers, craftsmen, and persons in charge correspond to different ways of operation. The hierarchy of operating rights ensures an orderly and controllable system.
A "win-win" for production capacity and quality
The accuracy of the recipe affects the quality of the product. The main material in this project is measured using Multi-components Suction and Weighing Scale. A single scale can be connected to several raw material silos, with different raw materials merging into the same scale for metering, saving multiple scales and optimizing the plant layout.
At the same time, Multi-components Suction and Weighing Scale also has the function of high, medium and low speed regulation, during production, the system automatically adjusts the feeding speed, thus achieving the advantages of high metering and conveying efficiency and high metering accuracy.
Multi-components suction and weighing area
One of the problems that many plastics manufacturers face is the wide variety of products and the large number of recipe variations, often with a large variety of raw materials and small quantities. For this type of raw material, which needs to be added in small quantities, auxiliary material dosing systems can automate and simplify the tedious problem of small batching.
Auxiliary Material Dosing System
Compared with Multi-components Suction and Weighing Scale, auxiliary material dosing system has a small dosage volume in a single batch, but allows for multi-batch proportioning to achieve small batches with high precision.
The flexible choice of different processes and equipment, for which ONGOAL provides process design and equipment selection, leads to a "win-win" situation in terms of capacity and quality.
Green is the goal of China's high-quality development, and fully biodegradable plastics, as one of the important means of green, low-carbon sustainable development, are becoming increasingly relevant to people's lives through PLA straws, biodegradable plastic bags, disposable tableware and more.
As an integrated service provider of material handling systems, ONGOAL provides one-stop solutions for customers and is committed to solving their practical needs and moving together into a new era of digital production.
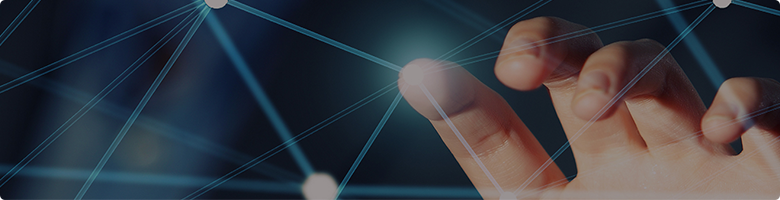
